How to Future-Proof Your Supply Chain
Best Practices and Recommendations for a Resilient Supply Chain
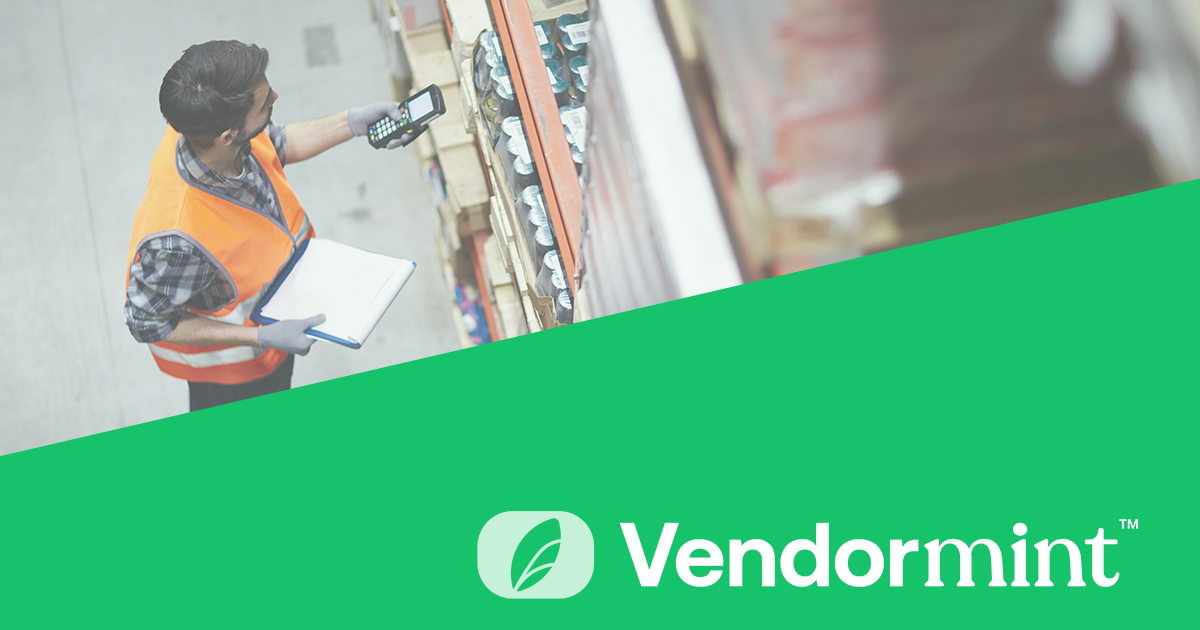
In volatile economic times, ensuring your supply chain flows in the most efficient way is vital. A sub-optimal supply chain can lead to retail deductions, out-of-stocks, and OTIF non-compliance—all of which will impact your bottom line.
Here are some best practices for ensuring your supply chain can handle sudden changes, stay compliant with new OTIF standards, and meet your revenue goals.
Proper Logistics Training
Most of the time, your third-party logistics companies, warehouses, and distribution centers use two types of teams: the core team and short-term workers. The core team consists of full-time employees who typically have been with the company for many years. These are skilled professionals who manage short-term and seasonal workers. Logistics companies hire these employees for a short period, and they are mostly part-time.
As the name suggests, day workers are fast employees, so there is little onboarding time. Whereas your core team will have lots of experience and training, day workers must begin their duties very quickly. This means that onboarding and training need to be lightning-fast.
Ensure you find a 3PL with a strong core team that can train day workers within 15 minutes of contracting. Day workers should know how to unload and palletize properly and efficiently within this timeframe.
Additionally, ensure that all forklift drivers have the proper training and certifications. Accidents will happen, but training will help reduce these incidents and avoid costly (and painful!) mistakes.
Lastly, ask your 3PLs and warehouses to consider segmenting their core teams by retailer. Each retailer will have its own carton, pallet, packaging, and labeling requirements, as well as on-time, in-full standards, such as OTIF, ORAD (Kroger), and OTFR (Target).
Warehousing and Transportation Software
Most 3PLs and warehouses use software to confirm orders, and brokers and transportation companies use technology to confirm shipping dates, appointments, and arrival times. Warehouse and transportation management systems software also integrate with EDI and allow for better shipment tracking.
The vast majority of brick-and-mortar, big-box retailers require EDI integration, routing systems, and communication from your 3PL’s WMS and TMS to create a resilient supply chain. It’s a best practice to hire well-trained supply chain management professionals in-house to work on your orders and communicate with each link along the chain. SCMs can confirm POs, route orders, and track shipments. They can also work on deductions disputes, document management, and EDI compliance as these issues arise.
Small and mid-sized retail suppliers may not be able to afford in-house SCMs, so if this describes you, research the capabilities of a 3PL and make sure you find one that knows how to comply with your retailers’ standards.
Paper versus RFID
While many links in the supply chain are digitized, some 3PLs still rely on paper. Paper has some excellent qualities compared to digital formats, but there are some best practices for this method.
For starters, paper documents in logistics must be bilingual to accommodate all workers. Many day workers do not speak or read English well, so bilingual documentation can ensure they are still effective workers.
Paper documents must also contain clear handwriting and legible details, such as numbers of cartons and date/time stamps. Make sure that your 3PL keeps their documents readable by OCR technology so that should OS&D or OTIF fines occur, you can effectively dispute them with the right technology and expertise.
If paper sounds too scary and unreliable to you, consider a 3PL that uses RFID technology to track shipments and loads. Walmart, in particular, led the implementation of radio frequency identification scanners in its supply chain at its DCs and revolutionized modern retail. RFID scanners can reduce mismatches on PODs and BOLs and connect directly with your EDI data to provide accurate ASNs with verified SSCCs. Should OTIF fines, deductions, or chargebacks occur, you can use these data to dispute them. (Need to look up an acronym? Find it here: Supply Chain Alphabet Soup.)
Additionally, RFID technology makes it easier to track cycle counts. RFID scanners can enable you and your 3PLs to check inventory quickly, efficiently, and more frequently. While paper systems may restrict your cycle counts to four times a year, RFID can enable you to perform inventory counts four times a month.
Standard Operating Procedures
SOPs are vital to a flowing supply chain. If you begin to see OTIF non-compliance or issues with your supply chain performance, you must implement documented procedures for your 3PLs, transportation, and warehousing. Document the ready-to-ship request process and ensure your 3PLs know the compliance requirements for each retailer. Some retailers have larger delivery windows than others, and all have different routing steps.
Your SOPs should be product and retailer-specific. SOPs should contain your retailers’ standards for cases, units, cartons, palletizing, packaging, labeling, and, if applicable, temperature regulation. For example, some retailers require labels to be placed 1.25 inches from the right edge, while others prefer 2 inches from the edge. Document how your retailers format their labels. Do they need to include the PO number? The casepack number? Be specific.
SOPs should also include documentation policies, again specific to each retailer. For example, some retailers require individual BOLs for each ship-to location, while others allow for just a master BOL. If you ship to a consolidator, you can combine your individual BOLs into a master document.
Lastly, ensure that your SOPs include clear, step-by-step instructions for routing orders specific to your retailers and their individual systems. Every retailer has its own routing method, so ensure your logistics companies know precisely how to confirm and route orders. Some retailers require you to check your ship status the next day to ensure the shipment arrives on time. Instruct your 3PL to re-check ship statuses, export the information, and file it in case of deductions. Some retailers update their ship statuses in emails as well, so ensure your 3PLs check their inboxes and spam folders.
Audit Your Third Parties
Auditing your logistics and shipping partners is crucial for oiling your supply chain and ensuring it’s future-proof. Learn from past mistakes to adjust for future uncertainties. If you consistently see OTIF fines, short-ships, or mispacks, it may be time to shop for a new partner. Alternatively, you may want to pass these fines on to your logistics company to help recoup costs. Or, you can dispute the deduction.
Additionally, check your documentation to ensure that your third parties are charging according to their contracts. Review invoices, BOLs, and service level agreements (SLAs) and check them against what you originally agreed to.
Speaking of documentation, it is vital that your third parties correctly and accurately document each step in the product’s lifecycle from the source to the store. This includes signing shipping documents like BOLs and PODs and clearly marking quantities and PO numbers. Improper documentation causes chargebacks and makes disputing invalid deductions difficult.
Recommendations
To sum up, a well-oiled, standardized, tech-reliant, resilient supply chain can help avoid costly deductions and non-compliance fines, enhance replenishment and instocks, and overall reduce waste and lost revenue.
We recommend that you do the following to optimize your supply chain:
- Properly and thoroughly train your 3PL core teams to train day workers in less than 15 minutes. This ensures efficiency, effectiveness, and a smooth workflow day to day.
- Integrate your 3PL’s WMS, TMS, and EDI technology into your daily operations.
- Weigh the pros and cons of paper documents versus RFID scanners to ensure proper documentation.
- Create standard operating procedures specific to each retailer and its particular routing instructions, PO confirmation process, and packing and labeling requirements.
- Regularly audit your third parties and ensure they are running smoothly and meeting goals and SLAs, and if they aren’t, consider either a new provider or ask for remuneration from non-compliance fines.
Of course, all of this requires hard work on your part. So, find a service provider who can help! Let’s talk about optimizing your supply chain and ensuring compliance today. We have over 75 years of combined retail experience, including deductions management, operations optimization, and documentation management. Let’s get to work on your supply chain today.
More Posts
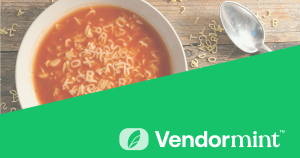
Digesting the Supply Chain Alphabet Soup
The supply chain world is an alphabet soup of acronyms and abbreviations! Use this guide to learn what ASN, OTIF, SQEP, and more mean.
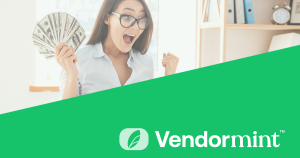
How Do I Dispute a Deduction in Synergy?
Did you know that not all Target deductions are valid? You can dispute invalid chargebacks in Synergy by following the steps in this guide.
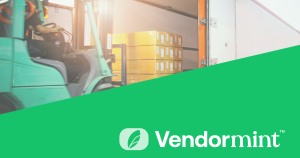
How Do I Choose a Shipping Option for My Retail Supplier Business?
From LTL versus FTL to Collect versus Prepaid, here’s how to choose the right shipping option for your retail supplier business.
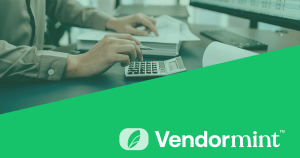
8 Foundational Steps to Effectively Reduce Retail Deductions
Learn 8 essential steps to reduce retail deductions, recover revenue, and protect relationships while improving profit margins.
When you realize
you're missing out
on all the insider info
Get in on the action and join the VendorWorld™ Newsletter—stay up-to-date with industry tips, tricks, and the latest trends.
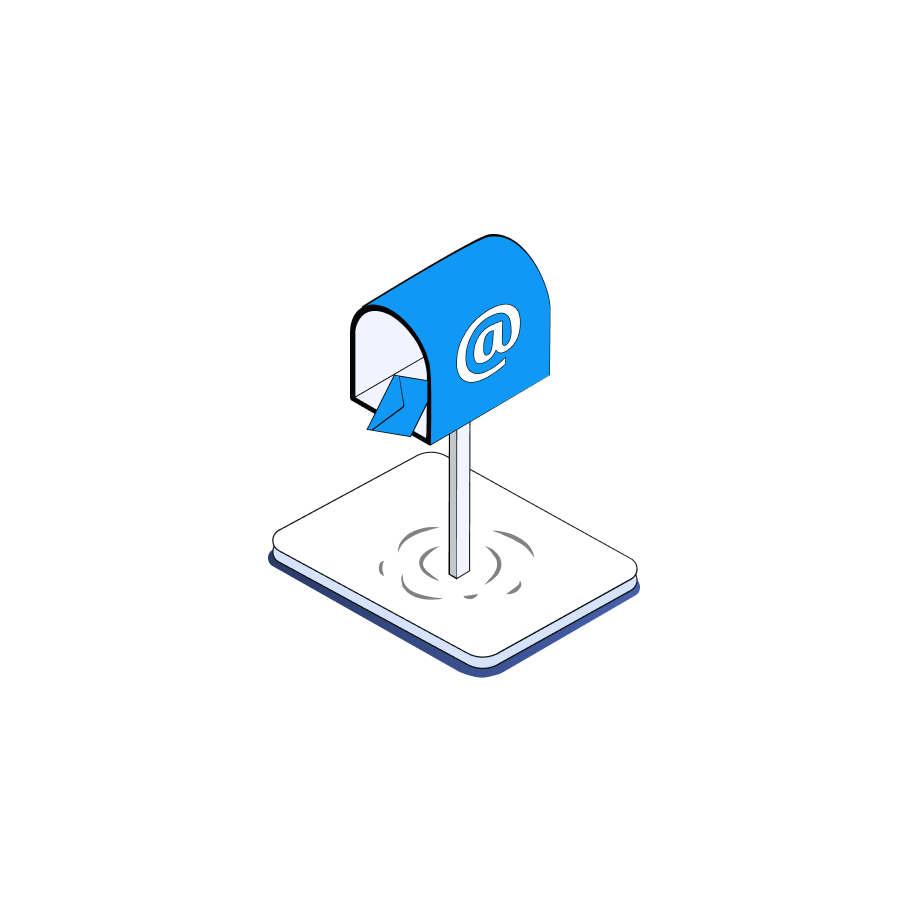